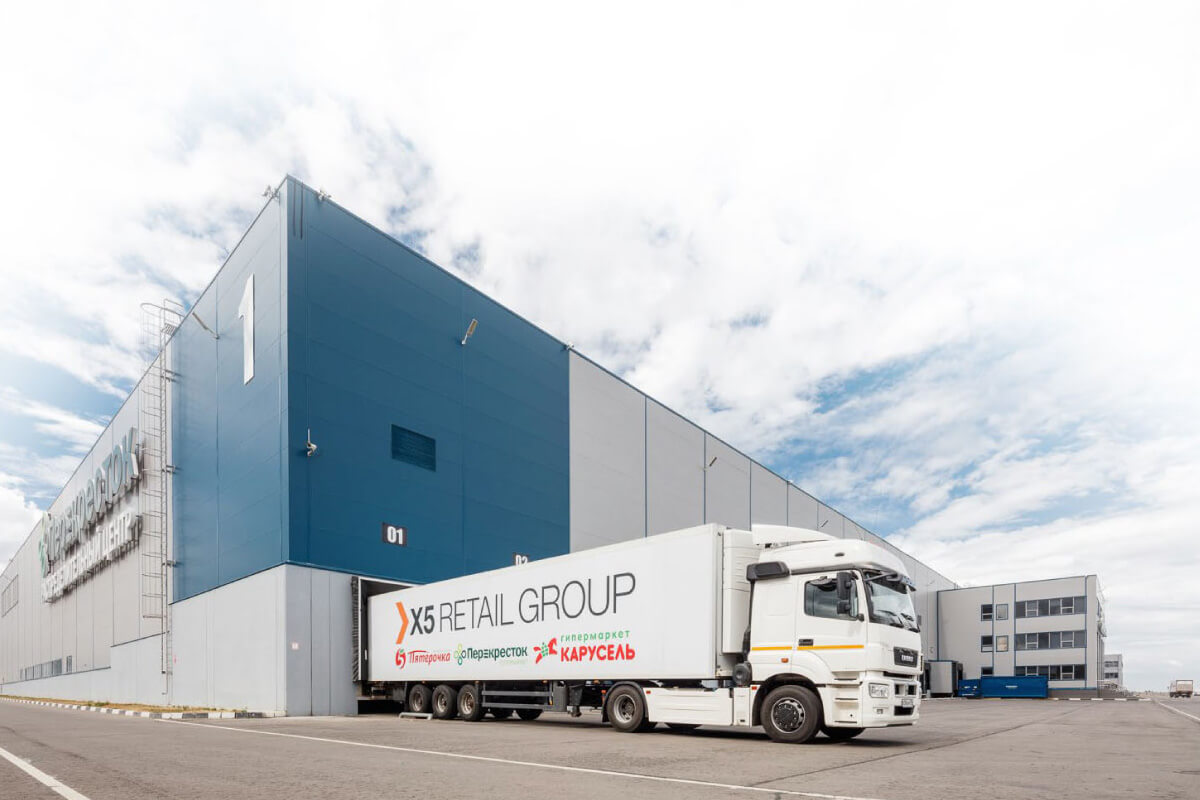
infrastructure
Logistics
We are developing our logistics operations to support the rapid expansion of our business. Pyaterochka runs its own logistics, while Perekrestok and Karusel share infrastructure. In 2017, X5 opened 10 new DCs with a total area of 249,079 square metres; we also closed six DCs with a total area of 72,632 square metres that did not meet our efficiency criteria. As of 31 December 2017, we were operating 39 DCs with a total floor space of 1.1 million square metres, providing sufficient coverage for the Company’s rapidly expanding operations.
X5 Retail Group’s company-wide SLT level (order processing based on timely deliveries) remained stable at 91.5%, while centralisation increased from 88% in 2016 to 93% in 2017.
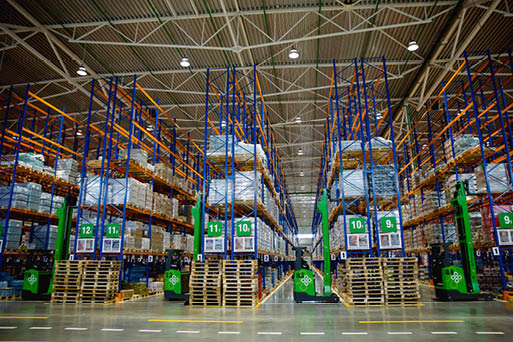
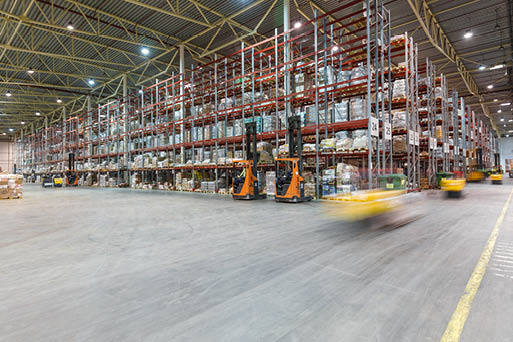
Logistics and Transportation Strategy
One of the key milestones achieved in 2017 was the adoption of a new Logistics and Transportation Strategy to 2025, which covers plans for the development of our logistics operations. While our logistics operations are divided to address the specific needs of different formats, the Corporate Centre together with the formats are constantly working together to share best practices, improve efficiency and leverage synergies.
The focus of the new strategy will be on reducing costs, cutting delivery times and ensuring the availability of a wide assortment of goods on our stores’ shelves. The strategy was developed to enable X5’s logistics to:
- Support the unique CVP of each retail format
- Respond to forecast demand through 2025 for each specific location
- Enable each format to achieve target market share, expanding operations based on the planned number of stores while reducing share of costs
- Allow formats to manage their own supply chain operations while in parallel seeking and implementing opportunities to achieve synergies
How we manage logistics
The X5 Corporate Centre is responsible for setting standards and monitoring performance of DC operations. It also aims to facilitate the sharing of best practices and technologies between formats, and it acts as a central resource for analysis and planning of the expansion of our logistics infrastructure.
All of our DCs utilise an automated warehouse management system (WMS) that includes features like voice picking and weighing technology. We are now testing new, innovative technologies such as radio frequency identification (RFID) tags and drone copters to monitor inventory status.
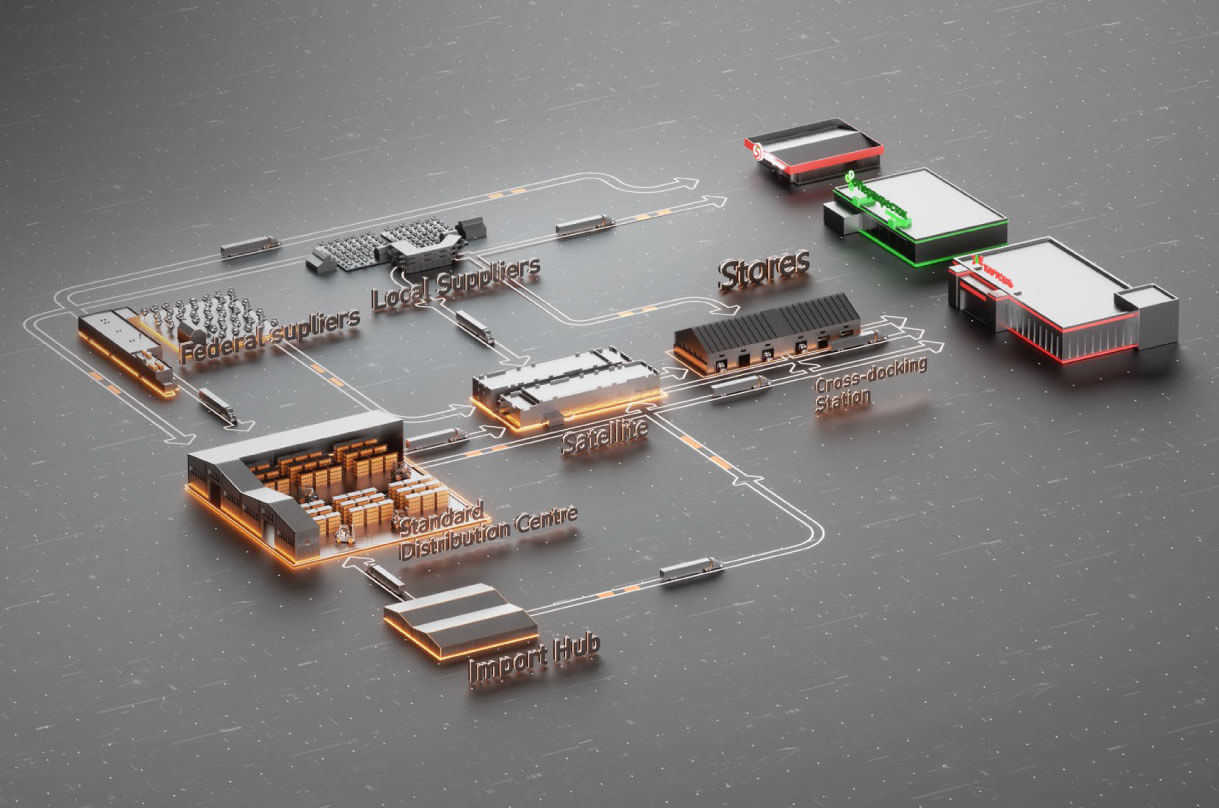
infrastructure
Pyaterochka opened nine DCs with a total area of 235,447 square metres and closed five RCs with an area of 69,632 square metres that did not meet X5’s strict efficiency criteria. While remaining the fastest-growing format in X5 Retail Group, Pyaterochka managed to significantly optimise logistics costs thanks to the increased operational efficiency of DCs.
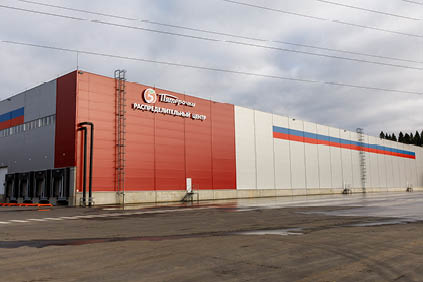
2017 performance highlights:
- Maximum DC throughput increased by 37% year-on-year, from 30.2 million boxes/week in 2016 to 41.3 million boxes/week in 2017
- Warehouse costs (RUB/box) continued to decline, decreasing by 21% year-on-year in 2017 from 12.9 RUB/box to 10.2 RUB/box
- Approximately RUB 3 billion in savings achieved through various warehouse cost optimisation measures, including streamlining staffing, cutting rental payments and reducing losses
Key highlights of 2017 included:
- Began introduction of new WMS from market leader Manhattan Association in order to improve operational efficiency and management
- Continued to develop multilayered logistics infrastructure, including improving the efficiency of import hubs in St Petersburg and Novorossiysk, as well as the development of cross-docking stations in remote regions
- Focussed on improving efficiency of transportation between own DCs
- Engaged staff in improvement initiatives, with special programme to seek employees’ ideas on how to increase the quality and efficiency of their daily routine duties. Ideas are grouped into five areas (security enhancement, workplace organisation, quality assurance, process improvement, resource consumption), and are then used to update warehouse and transport standards. All Pyaterochka DCs participated in this initiative in 2017
Inventory management
- Under the “Chain of Freshness” programme, we are developing a strategy for fruit and vegetable complexes that will combine import and domestic fresh produce supplies, accelerating the flow of goods from suppliers to stores through X5’s supply chain and helping to achieve higher quality while reducing costs
- Regular quality audits, introduced in 2016, were expanded to include elements of the BRC Food Safety Standard regarding the storage and transportation of goods. This included staff training, internal cross-audits of DCs, and the full-scale implementation of the BRC Food Safety Standard at the Lobnya DC
- The development of multi-use containers for fruit and vegetables continues, helping to minimise losses and simplify operations in warehouses.
Distribution centres and supply chain optimisation
- Our Logistics and Transportation Strategy utilises the Llamasoft platform to support its goals of maintaining the Company’s growth in its current locations and to provide for expansion into new regions, while optimising storage and transportation costs. This software enables us to develop our supply chain based on an analysis of a wide range of factors, including planned store openings through 2025, the location of key suppliers, DC inventory levels, the operational efficiency of warehouses, transport tariffs, the level of supply centralisation and the assortment matrix
- Using data analytics, we are now able to identify locations and plan the size of new DCs based on the potential volume of stores to be serviced
Plans for 2018
- Further integration of the WMS system, with completion planned for 2018
- Ongoing monitoring of innovations that may advance warehouse and transportation technologies
- Roll out intelligent inventory monitoring system that utilises RFID tags and drone copters to track inventory levels and quickly identify improperly stored items
Our larger-format stores share logistics infrastructure that is fine-tuned to their needs. As of the end of 2017, Perekrestok and Karusel were operating 12 DCs.
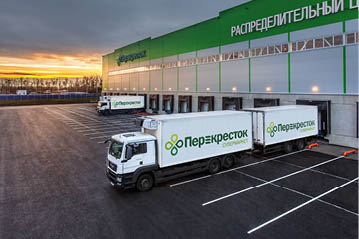
Key highlights of 2017 included:
As part of X5’s Logistics and Transportation Strategy, Perekrestok and Karusel are implementing four key projects:
- Using big data to improve the choice of locations for new DCs based on demand and store locations
- Integrating plans with suppliers to enable end-to-end supply chain management
- Implementing a WMS together with Pyaterochka
- Optimising layouts and designs of regional DCs
In line with Perekrestok’s CVP, which focuses on quality of goods and services, as well as freshness, development of the supply chain will concentrate on further improving shelf availability of goods in stores.
Inventory management
Our inventory management efforts in 2017 included:
- Reducing inventories, order fulfilment timing and increasing the availability of goods in stores
- Improving DC productivity: we managed to bring DC running costs down by 5%-7% thanks to efficiency measures
- Implementing JDA for 90% of volumes, which had a significant effect on reducing inventory levels. The JDA delivery system has enabled us to start making same-day deliveries to our stores in and around Moscow
- Enhancing synergies with Pyaterochka for shipments to remote regions (shared use of transport)
- Implementing same-day shipment of goods (except for the DCs in Kosulino and Samara)
Distribution centres and supply chain optimisation
- We launched a new DC in Yekaterinburg in the Urals (Kosulino DC, with an area of 13,700 square meters), which helped to optimise logistics for our regional expansion
- We helped to increase the efficiency of Perekrestok’s regional supermarket model, helping suppliers in the regions work directly with the new Kosulino DC. This enabled us to reduce logistics costs from RUB 38 per box in Q1 2017 to RUB 26 per box in December 2017
- We further developed direct imports through our import hubs in Novorossiysk and St Petersburg
- We introduced BT-9 temperature monitoring technology, which provides real-time temperature and humidity data all the way from the supplier to the DC and then to the store
Plans for 2018
- Further development and optimisation of regional logistics efficiency
- Complete implementation of JDA for all turnover in H1 2018
- Further develop supply synergies with Pyaterochka for remote regions
- Increase DC productivity, including staff productivity, by implementing new technologies, and focussing on improving the availability of goods
- Further develop direct imports, mainly for fruit and vegetables
- Launch a banana ripening complex at the Sofino DC in February 2018, ensuring the supply of bananas to the Perekrestok and the Karusel formats (starting with Moscow and the Moscow region)